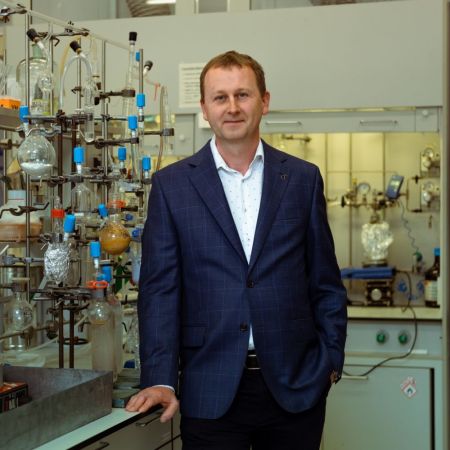
Although plastics don’t have the best reputation at present, they have fascinating properties. Modern society cannot make do without them. We all use them, and we’re not going to stop using plastics just like that. Why? The answer to this question follows in this interview with Professor Jan Merna, head of UCT Prague’s Department of Polymers. Merna also discusses trends in polymer research, new approaches to 3D printing, and why biodegradable polymers are not the game changer they might seem to be at first glance.
People commonly associate polymers with plastics, which do not have the best reputation with some in the general public. Why did you choose to study polymers in your professional life?
I became interested in polymers as far back as high school because they are cutting-edge materials. The study of polymers is actually the youngest branch of chemistry, next to the organic and inorganic branches. Just last year marked 100 years since chemists gained an understanding of the structure of polymers. There was hot discussion in the early days of the field. There were no polymer chemists, so a couple of organic chemists came up with the initial idea to create a specialty in this area. Hermann Staudinger, who demonstrated that polymers are composed of high molar mass macromolecules, had to struggle for a long time against the entire chemistry community at the time to show that polymers are not clusters of small molecules but are huge macromolecules. Most renowned chemists thought that such large molecules could not be stable and must be clusters. They were mistaken, though Staudinger waited over 30 years after his initial discoveries for the Nobel Prize.
What I like about polymers and modern materials is that they have a range of different applications and that the topic itself is complex. In organic chemistry, we often synthesize a new substance, describe it, and that’s more or less the end of the process. But for polymer chemists, the polymer synthesis is often just the beginning of research work, because we are interested in the material properties of a synthesized substance and investigating what a substance might be good for in real life. Lately, we are also thinking more about end-of-life for materials; how to deal with polymer waste.
You mean recycling?
Yes, this is a very important topic. We in Europe collect most of our plastic waste and not much of it ends up in the environment, but the problem arises in other parts of the world where there is poor waste management. If plastics get into nature, one of the properties of polymers is that they are very resistant to degradation and can survive in the environment for hundreds of years before disintegrating.
Actually, the optimal solution would be to develop better systems for collecting and reusing plastic waste. This presumes careful sorting into individual types of plastic, because if we don’t sort properly, just mix different kinds of plastics together, melt them, and make new products, the resultant outputs won’t have good properties. However, proper sorting is not only difficult, but it is also expensive. Plastic recycling also can’t be performed on an infinite loop, because repeated melting degrades the polymers involved and there is a limited number of cycles before the polymers become unusable. That’s why current research is focusing on finding alternative to mechanical recycling.
Which is?
The crucial challenge for our field is finding an economical and energetically reasonable way how to get to monomers, which are the primary raw materials from which virgin polymer can also be produced. So far, there are solutions for selected polymers, e.g. polyethylene terephthalate or polymethyl methacrylate (that is, plexiglass), but the vast majority of these are polymers that are not used broadly. We would need to find viable and cheap solutions for polyethylene and polypropylene. Unfortunately, there is no viable cleavage site in the structures of polyethylene and polypropylene, and current technologies such as pyrolysis are not very selective.
Another research direction is the quest for new monomers for the production of polymers that could then be easily degraded, i.e. recycled chemically. The problem, however, is that since the 1970s, no new polymers have gained ground in the marketplace, mostly for economic reasons. We will see if a requirement for good degradability would hearken change and if these kinds of new polymers might have competitive properties in terms of strength, ductility, processing stability, and so on.
Does plastic waste in nature, despite being ugly, have other problems?
In general, polymers are non-toxic inert substances and are biologically tolerated. They do not harm us on their own and are not toxic. Body implants are made from polymers; tissue substitutes are made from silicone. We store blood for transfusions in PVC bags softened with phthalates. What we don’t know for sure is whether polymers cause any health risks in the form of small particles.
For example?
There is an existing hypothesis that microplastics can act as carriers of pathogens, but this risk exists for all microparticles in the environment. We have been living with synthetic plastics for at least 70 years, so microplastics in the environment are not a recent phenomenon. In the past, thought, polymer products were not stabilized as well as they are now. They used to decompose over shorter intervals, and so-called secondary microplastics were formed more easily (but from far fewer plastics were produced). The first mention of finding microplastics in oceans dates back to the 1970s, but this was not a fashionable topic of investigation back then. Due to plastic non-toxicity, the WHO does not recommended monitoring microplastics in water. Water purification technologies, however, can be highly effective in removing any particles, including microplastics.
What do you think about the fact that most plastics collected in yellow recycling bins across the Czech Republic end up in incinerators?
Fine by me. From a chemist’s point of view, this is definitely a better scenario than being out in the environment or in a landfill. Of course, I’m talking about plastics, which are difficult to recycle. Most polymers are made from oil, and human being burn 90% of oil straight away. So if plastics could serve as an intermediate material product and we could get part of the energy we invested in production back, why not? The exhaust fumes from incineration of most common polymers are not toxic and are similar to those of burning gasoline, i.e. made of carbon dioxide and water.
One of current research trends is the production of biodegradable polymers.
Yes, but even in this case, one must note that even if a polymer breaks down into something harmless in nature after some time, we lose all the energy we had put into its production.
I believe that for biodegradable polymers, a much better scenario for the end of a product’s life cycle would be to collect and recycle them, or, if recycling’s not possible, to incinerate them. For polymers from renewable sources, this would achieve a neutral carbon balance. If we can collect plastic waste, it doesn’t matter if it’s biodegradable or very stable since we still can transform it into something.
Are there any other hot topics for polymer researchers?
Right now, new 3D printing technologies that naturally lend themselves well to small-scale production are very hot. Specifically, I am referring to reactive 3D printing, where polymerization takes place directly during production (printing), where the resulting product has significantly better properties than what’s possible using classic 3D printing technology from polymer strings. We are investigating this at UCT Prague as well.
How do you polymerize during the printing process?
We use light, for example. We have a bowl with a transparent bottom, pour a monomer into it, and the light where it passes through starts the polymerization process. Then we move the product a little higher and the monomer will again flow under the product under development, and so on, until a completely compact, homogeneous product is created.
Can you also produce polymers that can react to external stimuli?
Yes, this is also an attractive direction for research. For example, we have polymers which macromolecules, when heated, change shape and, for example, pack into a tighter conformation. Macroscopically, this manifests itself in the form of shrinkage that we can use as a mechanical element, a trigger or a valve. The stimuli can be different: temperature, pH, or the presence of a specific chemical. There’s the potential for use in detectors or sensors.
Your department is historically connected to the topic of hydrogels. Is there still room for development in this direction?
Hydrogels belong to the group of materials that are attractive because they can be used in medical applications. Due to the softness and pliability of hydrogels, they are also used as substitutes for human soft tissue, beside traditional use as contact lenses developed by Otto Wichterle. Soft tissues are composed of natural protein macromolecules, i.e. they are also polymers, just perfectly produced by nature.
You are particularly interested in research of catalytic polymerizations. What is that?
You’re referring to coordination polymerization, but we ourselves also use the term “catalytic polymerization” for better comprehension. For most polymerizations, we need a substance that forces a monomer to transform into a polymer. In catalytic polymerizations, the agent that forces this transformation is the catalyst. We currently use such processes to produce the majority of polyethylene and polypropylene that together comprise the majority of plastics. The basic procedure has been around for decades but was initially unviable. As catalysts gradually developed, production increased, and today, these basic polymers are produced so well and so efficiently in terms of pricing and properties that they are replacing other polymers used in traditional applications.
Can you give us an example?
For the production of foils, e.g. for shopping bags, softened polyvinyl chloride was used most often in the past. Polyethylene is now used because not only is it cheaper, but its production is also more ecological. Modification of polyethylene and polypropylene properties for other application is definitely still a promising direction of research.
In academic research, the search for even more active catalysts is not our greatest concern because we can produce a lot of polymers cheaply enough. Instead, current research is directed towards the possibilities of depolymerization and investigating whether we will be able to selectively split a polymer into pieces and turn it into new material. In our research group, we focus on chemical modifications of polyethylene and we use one specific type of catalyst, the so-called chain walking catalysts. In the case of classic industrial catalysts, a monomer molecule sticks to the end of a growing macromolecule, and this is how the chain lengthens linearly. The catalysts we use are extraordinary in that they can jump back and forth along a polymer chain and start its growth again from a given part of the chain. The result is a macromolecule that is not “straight” but highly branched, and this completely changes its properties.
How?
For example, polyethylene and polypropylene are typical plastics and are hard materials, but if we branch them, we can make them into materials that have the same properties as rubber. Our next endeavour is to build polar groups into polyethylene chains. This is one of the biggest challenges in current catalysis. Fortunately, our catalysts are toleranteven to polar substrates, and this lets us to prepare special polar-non-polar macromolecules from which polymer nanoreactors can be constructed, to name one example. This means we are moving from commodity materials to chemical specialties.
Does your research group currently collaborate with commercial partners?
We have collaborated with Synthos for a long time. Most recently, as part of a two-year project, we jointly developed a new type of elastomer not based on butadiene polymers (normally used to make rubber) but on cheaper polymers based on ethylene.
You said that the vast majority of polymers are made from petroleum. How much plastic is produced from renewable raw materials?
Less than 1%, and the production costs are usually higher, so an increase in production is not very rapid. This is nicely described in the article “How green are green plastics?” To make a long story short, we use more energy to make environmentally degradable polymers than to make synthetic polymers. Which may not be problematic in principle, as long as fossil fuel energy isn’t required. So if we get to a future scenario in which non-fossil fuel energy sources are not a problem for us, this is one of possible path forward. We are still far from this ideal, however.
For the future, it should just be necessary to shift our point of view about options. In our group, we have investigated the use of carbon dioxide as a starting raw material for preparing polymers, for example. We overcame CO2’s low reactivity by adding a second, more reactive monomer and a suitable catalyst. The result was polycarbonates, which are otherwise produced from highly toxic phosgene. This kind of chemistry is not only more sustainable, but it can improve safety. So far, however, catalysts are not effective enough for industrial scale production, but this also used to be the for the aforementioned ethene polymerization catalysts in the beginning of their development.
You have been head of the Department of Polymers for over two years. Where do you want to lead the department?
I have no desire to tell people what to do. On the contrary, I would like them to be as independent as possible in their research. As a leader, what I can and want to influence is what kind of people will work here. We are currently witnessing a generational transition. Half of my colleagues are at an age when they wouldn’t have to show up tomorrow if they didn’t want to. Fortunately, they are kind-hearted, helping us here and passing on their experience to younger colleagues. It’s up to me to find us quality replacements for the future.
At first, I was sceptical that this could be possible, because we all know how basic table salaries are set here at UCT Prague. How to tell a potential candidate from abroad that their salary will be only higher if they find grant funding? Just 100 km away from Prague, candidates can get an adequate guaranteed salary (several times higher than here) for the same work. The number of students studying in materials programs is not large enough to ensure a big enough pool of doctoral students to meet our near-term needs for qualified research staff.
Nevertheless, we managed to recruit one former graduate who had completed several postdoctoral stays abroad, and a Marie Skłodowska-Curie Postdoctoral Fellowship (MSCA) facilitated his return. A young Ukrainian colleague also found employment with us via a similar MSCA grant for Ukrainian scientists. A year ago, in cooperation with the Institute of Organic Chemistry and Biochemistry of the CAS (Academy of Sciences of the Czech Republic; IOCB), we managed to recruit a married couple of chemists who had previously been at other top research groups. In Prague, they both got the opportunity to start their own independent careers, Dr. Gonsales at UCT Prague and her husband at IOCB. Working together as institutions, we try to provide them with excellent research facilities. Last but not least, I am pleased with the current cohort of young researchers who are slowly evolving from their junior status and are starting to succeed in getting their own grant-funded projects. The situation is therefore developing more optimistically than I had initially thought was possible.